Britain: Home of the tractor
The UK doesn't just produce world-beating cars. We visited the New Holland tractors factory, a leader in global tractor production
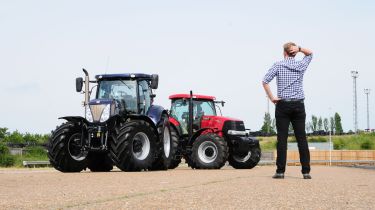
The UK is on a roll. With car sales continuing to rise, car production is hitting new heights, too. British-built models like the Nissan Qashqai, Jaguar XF and Range Rover are right at the forefront of a booming automotive business –but cars aren’t our only success story.
What you may not be aware of is that we’re also leading the way when it comes to tractors. The New Holland Agriculture plant in Basildon, Essex, produces hundreds of unique tractors every week for export across the globe, and welcomes 4,000 visitors a year. Customers flock to the site to choose their dream tractor from up to 10,000 configurations. To celebrate the diversity of UK industry – and fulfil a childhood dream – we took up an invitation for Auto Express to visit the Basildon plant and get our hands dirty by helping to build a new tractor, then take a test drive.
The New Holland factory – owned by CNH Industrial, headed by Fiat boss Sergio Marchionne – is this year celebrating its 50th anniversary, having moved to the 100-acre Essex site way back in 1964.
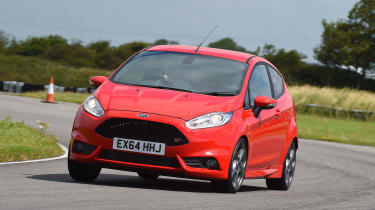
Since then 1.6 million tractors have rolled off the line, from the early days of Ford ownership, through the nineties when Fiat held a controlling stake, right up to the present day and CNH Industrial’s growth. But what’s the secret of its success? And why have bosses kept faith in the UK through the recession?Andreas Klauser, CNH Industrial chief operating officer for Europe, the Middle East and Africa, told Auto Express: “We have expertise in the plant and in the supply chain around here. We don’t want to move. The great heritage we have here is very important to us. We evolved into New Holland and it is a clearly recognisable tractor brand all across Europe.”
• Entrepreneur builds private toll road
Just as Klauser and CNH need the UK, so the UK needs the company. A staggering 90 per cent of the machines that roll off the line in Basildon are sent around the world, whether that’s to Europe, the US or less mainstream markets such as Paraguay or New Zealand. That makes New Holland one of the top 15 export companies in Britain with its 14 tractor ranges being sold in 120 countries.
Klauser added: “This is a very important company to the UK balance of payments and Basildon is an important global marketplace. It’s part of Basildon – it’s the home of tractors. The big focus is to continue world class manufacture and whatever is needed will be invested.”
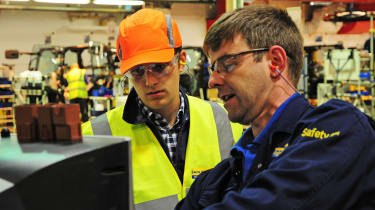
Our job for the day was to get involved in six of the production processes up and down the 2km of assembly lines. But first, we had to get dressed for the part, donning a hi-vis jacket and a hat to complement our New Holland overalls and thick boots. And it soon became apparent that we weren’t just here to make up the numbers. In the factory, there’s a constant stream of activity but also a calmness and focus among the workers – this is something CNH Industrial has actively worked on.
Over the past five years, it’s made £15million worth of savings through noise reduction, cleanliness and efficiency. Next, bosses hope to reduce noise further across the whole plant to make it an ear protector-free zone, too.
So what’s it like working in that environment? Where better to start than with the powertrain?
Our first role was to help fit the huge engines to the transmission. These engines, imported from the company’s other sites, range in output from 120bhp through to 270bhp, and we help screw the bolts and driveshaft into position. At the touch of a button they’re sent on their way as driverless flat-bed robots, patrolling the factory floor, come and pick them up.
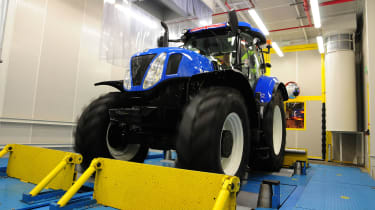
The next time we see the assembled parts, they’ve been fitted with the suspension and spray painted black. Here the joints are greased and tanks filled with diesel – with three tractors being built at the same time on the moving floor of the production line, it’s difficult to keep up.
We can see how these processes have barely changed over the past five decades, but at our next stop in the factory, it’s clear just how far UK tractor production in the 21st century has come.
The cabs are now fitted with a comfortable seat surrounded by hi-tech gadgets, touchscreen sat-navs and air-conditioning. Our job is to insert the switches into the C-pillars before wiring them up and snapping the C-pillars on to the cab. A clever light system tells you which buttons to fit where as each order rolls along the line.
• Speed limit for lorries to increase
Just across the aisle is the next stop – the quality gate – where we find out if we’ve been doing the job properly. Armed with a tablet linked to the order system, we circle each tractor looking for faults as it rolls past. A computer system logs problems that dealers or owners have found as tractors have been delivered, and these are added to the checks to make sure the same factory mistakes aren’t repeated.
Once the tractors have passed through quality control, the enormous wheels with their chunky tyres are fitted. We’re let loose with a wheel gun and allowed to do our best impression of a Formula One pitstop, only on a slightly larger – and much slower – scale.
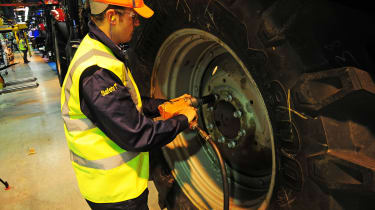
From here, the tractors can move under their own steam, and after one final quality check, they head to the rolling road – our final stop of the day. The Basildon facility houses two new bays for testing to ensure each tractor is ready for action. We go up through the gears, try the rear tool – to whicha plough might be fitted – and test the autonomous systems, plus the drive on each of the four wheels.
Once all this is completed, our tractor gets the green light and it’s parked up next to the rest of the completed vehicles – job done. Each New Holland tractor takes around 15 hours to build, spread over a day and a half, with staff at Basildon making an average of 100 per day.
After just a few hours on the factory floor, it’s clear to us that with this kind of work ethic and modern thinking, UK tractor production will continue to go from strength to strength - just like our car industry.
...and we take the wheel
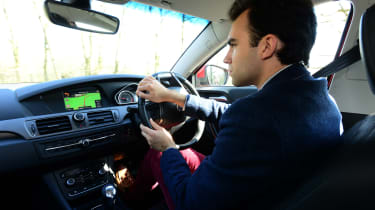
For many children growing up in towns and cities, the best thing about visiting a working farm attraction wasn’t the fresh air or the animals. It was the toy tractor in the gift shop.
So it was a dream come true for me when I climbed aboard the special-edition New Holland T7.270 Auto Command Golden Jubilee.
The plush cabin is more high-end luxury car than farming tool and the air seat effortlessly soaks up the rough terrain. There’s an option of driving the tractor with pedals, buttons or a joystick, and it was great fun racing up to 30mph with the massive tyres booming away behind.
The turning circle is tight and with the air-con on full blast, I gave serious consideration to a change of career. Even though I’ve grown up, there will always be something special about driving a tractor – and I’d certainly add this one to my dream garage line-up.
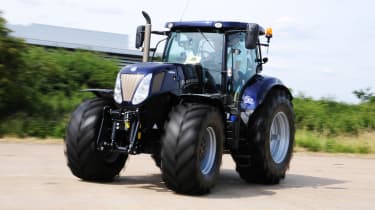
Essentials: T7.270 Auto Command Golden Jubilee
Price: £149,224Engine: 6.75-litre 6cyl dieselPower: 269bhpTorque: 1,160NmTransmission: CVT automatic, four-wheel driveTop speed: 50kph (31mph)Equipment: Cruise control, electronic parking brake, active stop/start, leather, Bluetooth, auto-guidance
Find a car with the experts